Exploring the Applications of Flexo Printing in Packaging
Flexo printing, also known as flexographic printing, has many unique advantages and has experienced rapid development worldwide in recent years. With the emergence and advancement of various new technologies, materials, and equipment, the application range of flexo printing has been expanding, particularly in the packaging industry where it demonstrates distinct advantages.
Flexo printing possesses unique advantages in terms of environmental friendliness and low cost. As people's environmental awareness increases and flexo printing technology continues to improve, coupled with new market demands, the application scope of flexo printing has rapidly expanded, thanks to the efforts of professionals in the flexographic printing field.
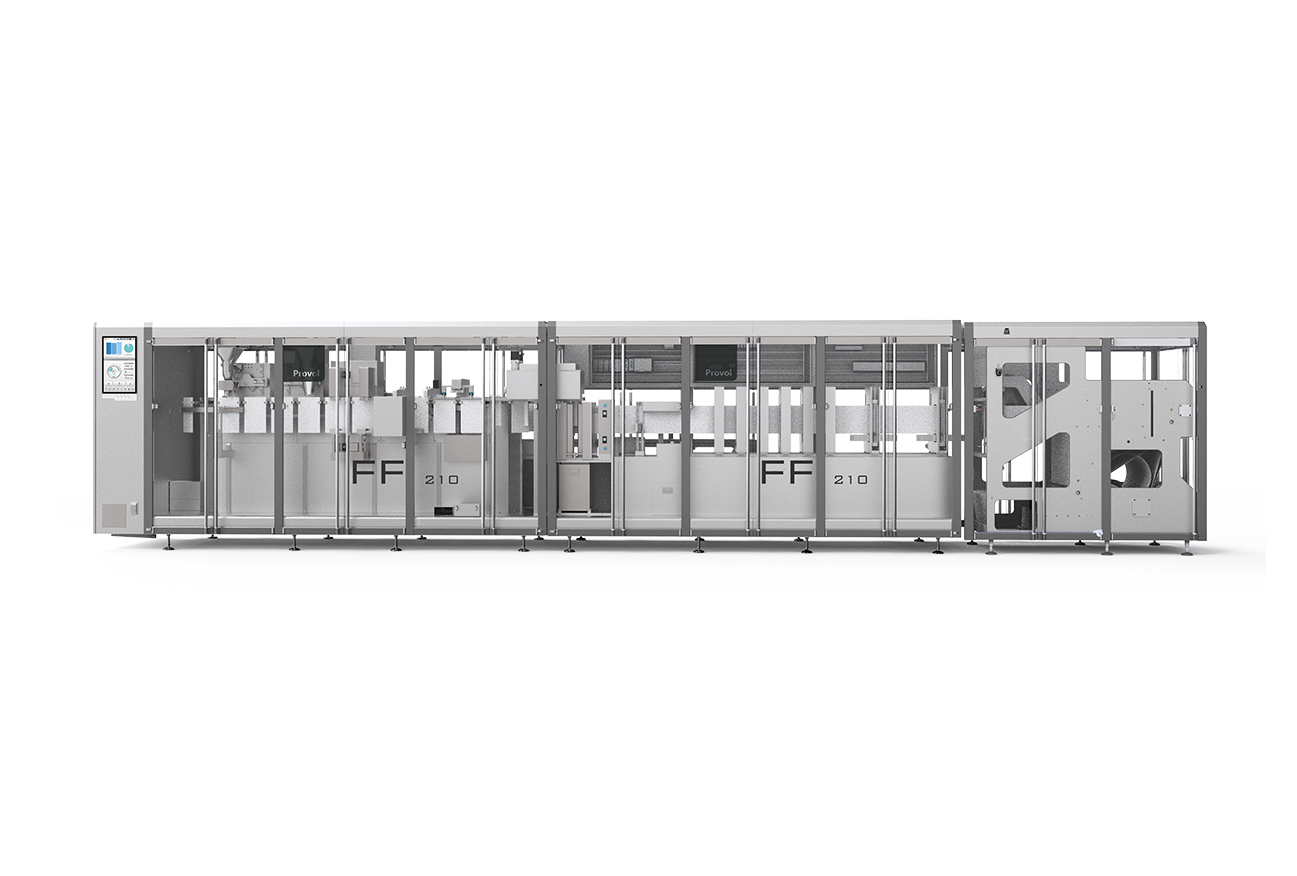
Flexographic printing has many benefits and is much faster than traditional gravure printing. Flexographic printing is fast, and modern flexographic presses can even reach speeds of over 600 feet per minute, far exceeding past standards. This is a huge advantage for companies that are considering upgrading their equipment. Moreover, flexo presses feature a rotating print head that allows complex designs to be completed in a single print run, providing the user with more creative freedom.
Another advantage of flexo printing is its versatility. It can print on virtually any non-absorbent material, including porous, non-porous, flat, rough, absorbent and non-absorbent materials. Whether printing solid colors or patterns, flexo presses are up to the task and can achieve excellent color alignment on extensible substrates.
At the same time, flexo printing continues to offer advantages in medium- and high-volume printing. Despite technological advances, digital printing still cannot match flexo in terms of cost and speed. For customers who need to print large volumes, especially in the label business, flexo is the preferred choice. Even in small print runs, flexo can compete with digital printing.
Flexo presses can accommodate a wide range of substrates for printing, such as paper, cardboard, foil, plastic film, cellophane, recycled substrates and a variety of textiles. This makes it particularly suitable for printing text and graphics on bags.
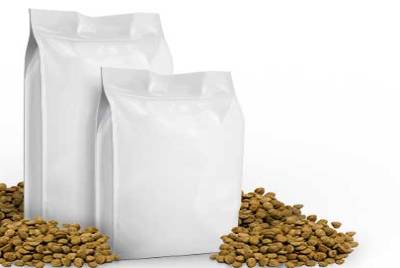
Flexo also supports a wide range of colors and can be used with both water-based and oil-based inks. This provides more options for different application scenarios and post-print processes such as heat sealing, lamination, etc.
In addition, modern flexographic presses are easy to use and maintain. Set-up and job changeover times are significantly shorter than in the past. Flexographic presses have a long production life and a satisfactory return on investment. Maintenance requirements are also relatively low as long as regular maintenance is performed.
In summary, flexo printing is fast, versatile, adaptable, has low operating costs, and is easy to use and maintain, making it an ideal choice for many industries. Whether printing in large or small batches, flexo printing meets the needs of users and delivers high-quality results.
Applications of Flexo Printing in Packaging
Flexo printing has achieved significant success in various packaging markets due to its unique technical characteristics. The main applications can be observed in the following areas:
1. Pre-printing on corrugated boxes
As people's living standards improve, the use of color corrugated boxes in product packaging has become increasingly widespread.
2. Label printing
Label printing is the fastest-growing sector in flexo printing. The growth in label printing is primarily driven by pressure-sensitive labels, which are rapidly replacing technologies such as die-cutting and direct printing. In the consumer goods printing sector, the shift from pressure-sensitive labels to in-mold labels and shrink sleeves will drive the transition from offset, gravure, and screen printing to flexo printing, thus promoting the overall development of the flexo printing industry. When pressure-sensitive labels transition to in-mold labels, the printing process also shifts accordingly to UV or water-based flexo printing.
Approximately 20-30% of consumer goods in the US market are presented in the form of flexible packaging. Surveys show that in 1996, flexo printing accounted for 75% of the soft packaging market in terms of film materials, a number that rose to 85% by 2000. The printing industry in the United States considers flexographic printing as the preferred choice for flexible packaging. As flexo printing dominates the North American flexible packaging industry, growth in this sector directly correlates to the growth of flexo printing.
Currently, in the domestic market, roof pouches have a wide range of applications, including liquid beverages and dry food products, with a particularly high demand for dairy products and fruit juice beverages. The packaging requirements for these products are also stringent: they need to comply with environmental standards, be pollution-free, and recyclable. Roof pouches, as a type of liquid milk packaging, have experienced significant growth in recent years, with an average annual growth rate of 30% since 1994. It is expected to continue growing at a high pace, reaching 13.5 million tons by 2005.